As rack heights extend upwards, so do costs.
Many furniture retailers are surprised by the fire protection requirements and costs when revising or expanding an existing warehouse, building a new facility or even acquiring a warehouse that was being used for furniture. There are a number of ways to approach fire compliance design issues, but experience has shown that skilled systems designers achieve fire protection compliance at substantially lower cost.
For this article FURNITURE WORLD asked nationally recognized fire protection code expert, Elley Klausbruckner to supply general practical information on fire protection requirements for furniture warehouses. Specific solutions require the design expertise of a qualified fire protection engineer and warehouse designer.
Due to rising land costs, the availability of high-rise material handling equipment and the need for large inventories to support sales, racked warehouses are expanding toward the heavens. Racked warehouses of 30 to 40 feet clear height and occasionally higher are common. The highest furniture warehouse of record in the USA is an automated warehouse at 106 feet clear height.
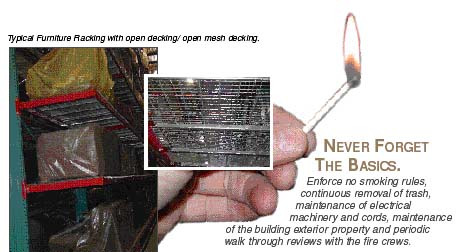
Increasing building height to achieve a desired storage capacity is much more cost effective than increasing the building footprint. This is true even when we factor in the cost of the fire protection systems needed to protect these facilities. Tall warehouses contain more goods per square foot, which in turn increases the potential property loss per floor area in the event of a fire. Property losses resulting from smoke and fire damage to inventory, in many cases, have surpassed the construction cost of the buildings. By definition, high piled storage is any storage over 12 feet. There are two major factors that affect any high piled storage warehouse:
•Commodity (i.e. what is stored/“burnabilty”/heat production of materials).
•Geometry (how the product is stored).
Commodity Classification
Commodity Classification is the practice of determining the “burnability” and “rate of heat produced” by a product. If commodity classification is done incorrectly, it will result in over-design (unnecessarily expensive) or under-design (inadequate) of the protection system within a warehouse or storage area.
There are five categories of commodities used by most insurance carriers and fire codes agencies; Class I-IV and High Hazard/Group A Plastics category. The Class I category includes the least burnable and heat producing products and High Hazard/Group A Plastics category includes the most burnable and heat producing products.
When providing information to the city and insurance carrier, it is very important to give a thorough description of what is being stored. The overall protection for a warehouse is typically based on the worst-case commodity. There are a few allowances in most codes for limited amounts of a higher hazard category products. For example, a warehouse can be classified as a Class IV warehouse with limited amounts of High Hazard/Group A. How this limited amount of the higher hazard has to be stored depends on the adopted code in the community.
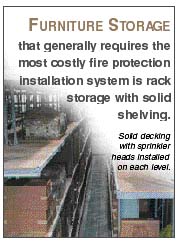
Warehouse Geometry
High piled storage is of great concern to fire inspectors, city plan reviewers, and the insurance industry because of the speed at which a fire can grow and spread, once a fire has started. A similar occurrence can be observed in the way a match will burn. It burns slowly or extinguishes in a horizontal position, but is consumed more rapidly and completely when held vertically. Rack storage, palletized storage, storage height, ceiling heights, etc., all affect the way in which a fire grows. When information is requested by fire plan checkers, inspectors, or insurance carriers, it is important to provide this information as accurately as possible.
The three most commonly used methods of storage are palletized/ floor storage, shelf storage and rack storage. The method of furniture storage that generally requires the most costly fire protection installation system is rack storage with solid shelving (typically large shelving greater than 32 square feet and less than 50% open). Pallets are considered part of the commodity, and not the rack. New inspectors and warehouse owners often misunderstand the role of pallets... a very costly mistake that can result in much higher fire protection costs.
If furniture on pallets catches fire, heat rises quickly, setting off sprinkler heads. Water cascades from the ceiling between the pallets down to the fire. That is why pallet loads set in racks without shelving are still considered racks without solid shelving.
When fires occur in warehouses fitted with solid shelves, heat is prevented from rising. Water from sprinkler heads mounted overhead is prevented by the solid shelves from reaching the fire which may then jump the aisles, spread horizontally and overwhelm the total system. That’s why rack storage systems with solid shelving typically require in-rack sprinkler systems (sprinklers installed in the middle of the racks) at every level of the rack. Alternative methods of storage, such as racks with wire decking, can be considered to reduce the cost impact of fire protection compared to solid shelves.
There are many other storage method options that can be considered based on specific site conditions. In a recent existing warehouse conversion to a furniture warehouse, low water supply and pressure made in-rack sprinklers less costly than installing a totally new overhead ESFR fire protection system which would have required a fire pump and large storage tank. A fire protection engineer, can evaluate alternate approaches to arrive at a cost effective and practical solution.
Local Code Agencies & Insurance Carriers
The following is a list of general guidelines to follow when information is requested by the local code agencies or insurance carrier:
Honesty and courtesy is the best policy. Building good relationships with insurance carriers and code enforcement agencies will help any business owner in the long term. Allow insurance agents and code enforcement officials to finish explaining their issues. Do not interrupt them with offensive or defensive comments. Intimidation does not normally work, and if it does, it provides only short-term relief. Remember, you have to live with these inspectors and agents for many years to come.
Apply for all permits when the warehouse is first built or when you are moving into an existing facility. A high piled storage permit is required by many local fire authorities these days. Do not let the permit lapse. Renew the permit, as required by the local authority (typically on an annual basis). If a permit is never obtained, or a permit has lapsed, the fire authority may require you to apply for a new permit and they may treat you as a new high piled storage facility (require you to meet today’s codes for high piled storage, not by the codes in force when the building was originally built).
Although some officials may give leniency to existing buildings or facilities, comments such as “we’ve been in this building forever” will not be persuasive when speaking with most code officials. Just because you did not tell the fire authority that the building was to be used for high piled storage when the facility was first planned or built, does automatically put the building in the “existing” category. If a high piled storage permit was applied for and renewed, the newer or current codes will not be applied to the facility, unless major additions/remodels/changes have been made. This permit is the only acceptable written proof you have that the building was originally designed and planned for high piled storage. These types of permits are based on the business, not the building. Even if a business that leased the building previously used it for the same purpose (warehousing of furniture), any new business moving in the same building is required to apply for new permits.
Provide detailed information when filling out the high piled storage information forms requested by the fire authority. Remember that the effectiveness of a fire protection system in controlling a fire depends on the commodity stored, as well as the geometry of the storage and building. Give them a detailed description of what you are storing and how you are storing it. It is a lot easier and cheaper to meet the code before the building is built and/or before you have moved in than after.
Almost all insurance agents and codes officials are professionals that are well versed in high piled storage requirements. However, if something does not sound right, or you need to further research alternatives to a requirement, it is all right to ask for requirements or inspection comments in writing. As a matter of fact, it is best to make it a company policy, so that the company representative dealing with the fire authority or insurance carrier has a valid reason to request their comments and requirements in writing
Hazardous materials permits and disclosure are under separate permits that may be required if chemicals, such as stains and touch up paints are used. Contact your local fire authority for information.
The best fire protection system in the world still requires the daily attention of management. Enforce no smoking rules, continuous removal of trash, maintenance of electrical machinery and cords, maintenance of the building exterior property and periodic walk through reviews with the fire crews that would respond to an emergency.
Elley Klausbruckner is a nationally known Fire Protection Engineer and a Hazardous Materials and High-Piled Storage specialist. She is a registered Professional Engineer and author of several publications including the “Uniform Fire Code’s Application Guide to High Piled Storage”. Klausbruckner & Associates clients are supported through all phases of the code compliance approval process with regional, state, and federal rules and regulations. She can be reached at elley@furninfo.com.
Daniel Bolger of The Bolger Group helps companies achieve improved transportation, warehousing and logistics. Questions can be directed to Mr. Bolger care of FURNITURE WORLD at dbolger@furninfo.com.